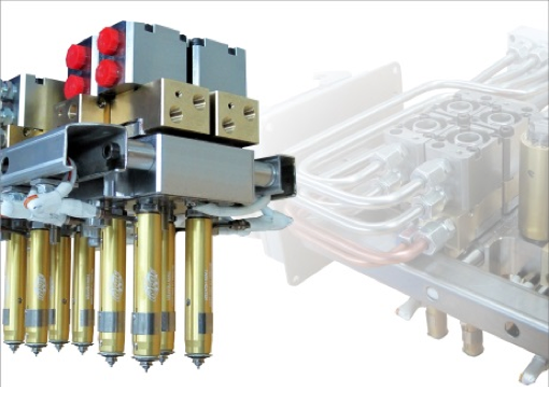
The hot runner system manufacturer INCOE® International Europe, of Rödermark, Germany, introduced innovations, concepts and solutions with advances in miniature hydraulics and fast color change. The Euromold theme for INCOE® promoted Global Technology Partnership to the Plastics Industry. The focus on solutions that improve efficiency, quality and process stability for customers with ease of use, were featured throughout.
HEM miniature hydraulics: Making optimum use of available space with high-performance
HEM offers proven performance with a compact footprint approx. 50 percent less when compared to conventional hydraulic cylinders. The design maintains all of the performance characteristics of much larger, bulky products.
HEM offers new opportunities for a variety of applications. For multi-cavity molds, the mold maker can now increase cavitation allowing processors to produce more parts without the need for increased machine size. The HEM hydraulic cylinders can be used in applications that were once confined to smaller, less powerful pneumatic cylinders, and increase valve gate performance.
In the automotive area, frequently large molded parts, such as door trim panels require large hot runner systems custom designed to the geometry of the unique molded part produced. Where needed, the designer can now realize injection points that are situated very close together. The latitude for selection of the injection points is broader overall, and this facilitates the positioning of slides and ejectors. The smaller milling areas strengthen tool stability for repeatable molding of parts.
NEW VIX Nozzle Tips: Trouble-free melt flow and Color Change
VIX nozzle tips offer “quick color change” with optimized channel geometry in the nozzle tip. Simplification of the tip design eliminates all of the “joints” on the surface of the channel where material can be negatively impacted. Multiple applications have used the VIX in North America and now European customers are acknowledging that with the new nozzle tip, the time and effort required for color changes are significantly lower.
SoftGate® Valve Pin Velocity Control; Proven, Repeatable Processing Performance now Worldwide
The SoftGate® valve pin velocity control for hydraulic valve gate systems was introduced to the European market at K2010, and then North America at NPE2012. With numerous applications running, the SoftGate® solution is now part of the INCOE® hot runner product program worldwide. The system has not only proven successful in the field, but has also helped to develop new areas of applications for a variety of injection molding processes.
SoftGate® valve pin velocity control systems resolve issues related to conventional hydraulic sequential molding. Issues such as poor flow characteristics leading to undesirable part aesthetic “ghost marks” and/ or gate blemish, are significantly reduced with SoftGate®. The key advantage for molders is in the gradual pin actuation, precisely timed as needed for optimized melt flow. |