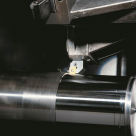
Significant reductions in machining costs for component manufacture can be achieved when replacing conventional steel with M-steel bar from Ovako, the company claims.
In the production of components, machining processes represent a considerable cost factor. M-steel can lower these costs facilitating higher cutting speeds and a non-interrupted production environment. With a claimed cutting speed of up to 30% faster than conventional steel, Ovako says that M-steel meets market demands for lower processing costs.
In many circumstances, tool life can be more than doubled when machining steel that contains inclusions. This not only saves on the actual machining time, but also reduced the true cost per component.
Used extensively for component manufacture in the automotive, energy, petrochemical, mining and general engineering industries, M-steel is produced in Imatra, Finland, by a highly automated serial production process, guaranteeing repeatability from cast to cast. As a result, there are no variations in the material, which eliminates the need to keep changing machine set-ups, such as tools, feed rates or cutting fluids.
At every stage of the M-steel production process the material is optimised to improve machinability, from raw material through melt, to casting, hot rolling and the final heat treatment. A key part is the modification and control of non-metallic inclusions with calcium treatment – important steps in secondary metallurgy which affect the composition and inclusion structure, as well as heat treatment.
Hard, non-metallic inclusions in conventional steel cause considerable wear of the machine tool, but in Ovako M-steel these are transformed to safer, calcium contained inclusions that are softer. They even create a beneficial lubricating film between the tool and the chip interface during machining. Additionally, the sulphur content is optimised to achieve the best possible machinability and toughness.
Harri Aakala of Ovako, Imatra, explains: “We can tailor material to suit individual customers, while at the same time share our extensive product know-how. Our ability to finely control the purity of our steel, its hardenability, its heat treatment and its machinability, is the key to M-steel products.
“Within our country sales offices experts can advise on specific material selection and capabilities so that the most suitable M-steel grade can be matched to a specific application. This allows customers to maximise their savings on processing costs.”
Central to the company’s manufacturing and supply operations is a Total Quality Management philosophy with full traceability from raw material through to customer supply. In the case of M-steels, in addition to the full spectrum of material testing, machinability tests are also carried out.
Ovako M-steel round and square bar is available in a wide range of standard dimensions and can be supplied cut to length to best suit customers’ machining centres.
Ovako is a leading European producer of engineering steel for customers in a wide range of industries. Production covers low-alloy steels and carbon steels in the form of bars, tubes, rings and pre-components. The company has production plants in 11 locations and sales companies in Europe (including the UK) and the USA. Ovako employs over 3,200 members of staff worldwide and total steel production capacity is 1.3 million tonnes per year. |